ORC System
Organic Rankine Cycle Solutions for Power Generation with Turbogenerators
The ORC (Organic Rankine Cycle) system is based on an innovative closed thermodynamic cycle for the flexible and distributed production of electric and thermal power. This ORC technology is particularly suitable for distributed generation close to the point of energy use, utilizing turbogenerators that convert thermal energy into electrical power without the need for water or vapor. Turboden's ORC systems exploit various heat sources to generate electricity and heat, such as renewable energies (like biomass and geothermal energy), traditional fossil fuels, waste heat from industrial processes, waste incinerators, engines or gas turbines. The absence of water and vapor in the ORC process eliminates the need for complex steam turbine systems, making the technology more compact, reliable, and easier to maintain.
Valorizing Thermal Sources with ORC Turbines
The innovative ORC technology allow recovering and converting wasted heat into electrical power using specially designed turbines. These organic Rankine cycle turbogenerators represent a flexible and efficient solution to valorize a wide range of thermal sources, both renewable and non-renewable, optimizing energy processes in a circular economy approach. The ORC turbines operate without the need for water or vapor, relying on organic fluids with favorable thermodynamic properties to drive the power generation process. This unique feature of ORC systems enables the efficient utilization of low-to-medium temperature heat sources that would otherwise remain untapped, contributing to increased energy efficiency and reduced environmental impact.
455
plants*1041.500000000001
MWe total1999
first plant delivered*63 plants are under construction
-
TURBODEN ORGANIC RANKINE CYCLE: WORKING PRINCIPLE EXAMPLE
-
TURBODEN SOLUTIONS FOR INDUSTRIAL PROCESSES
-
REDUCE YOUR ENERGY BILL BY GENERATING YOUR OWN POWER
THE RANKINE CYCLE
The Rankine Cycle is a thermodynamic cycle that converts heat into work. The heat is supplied to a closed loop, which typically uses water as working fluid. The Rankine Cycle based on water provides approximately 85% of worldwide electricity production.
The Organic Rankine Cycle's principle is based on a turbogenerator working as a conventional steam turbine to transform thermal energy into mechanical energy and finally into electric energy through an electrical generator. Instead of generating steam from water, the ORC system vaporizes an organic fluid, characterized by a molecular mass higher than that of water, which leads to a slower rotation of the turbine, lower pressures and no erosion of the metal parts and blades.
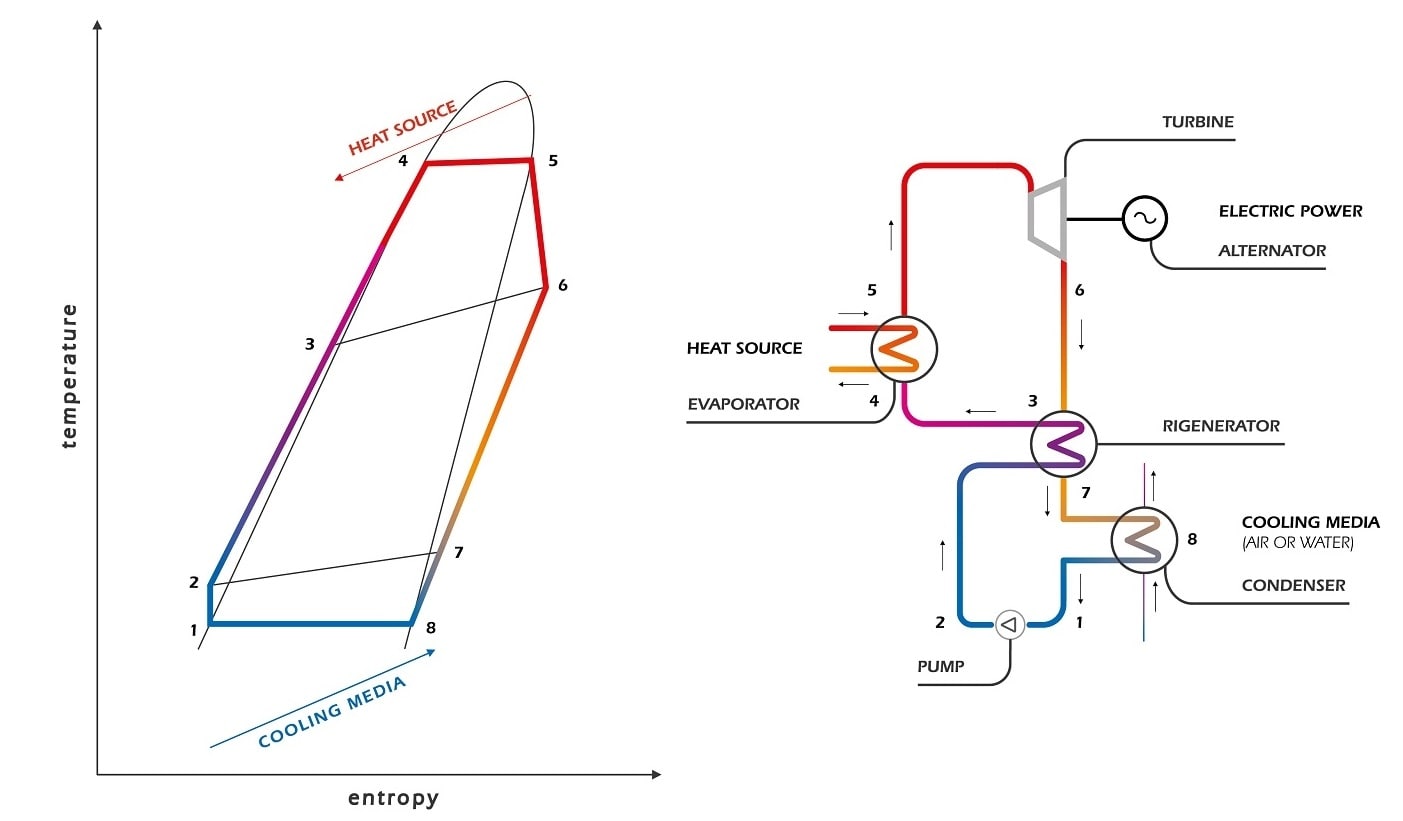
The ORC turbogenerator uses medium-to-high-temperature thermal oil to preheat and vaporize a suitable organic working fluid in the evaporator (4>5). The organic fluid vapor rotates the turbine (5>6), which is directly coupled to the electric generator, resulting in clean, reliable electric power.
The exhaust vapor flows through the regenerator (6>7), where it heats the organic liquid (2>3) and is then condensed in the condenser and cooled by the cooling circuit (7>8>1). The organic working fluid is then pumped (1>2) into the regenerator and evaporator, thus completing the closed-cycle operation.
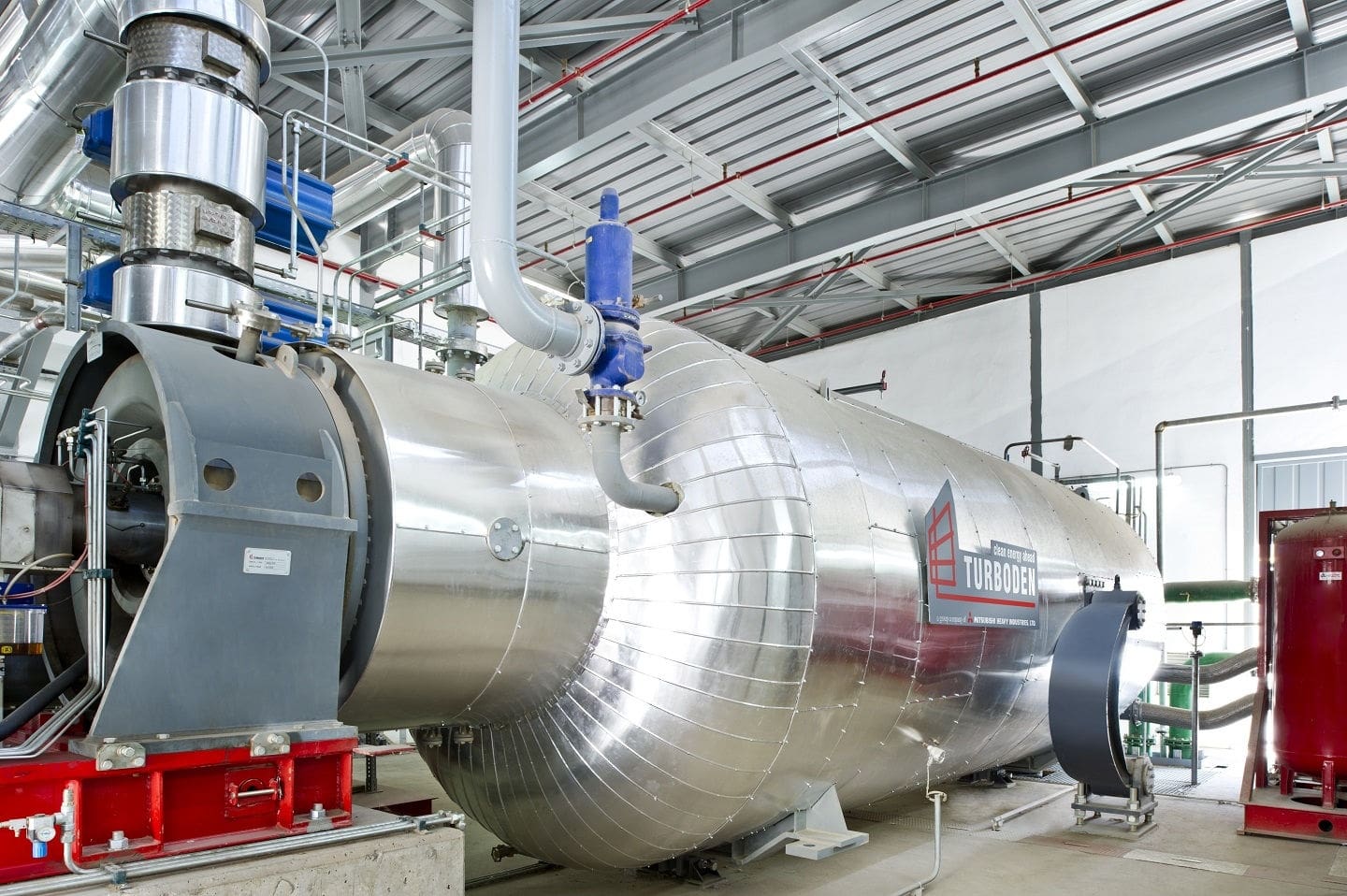
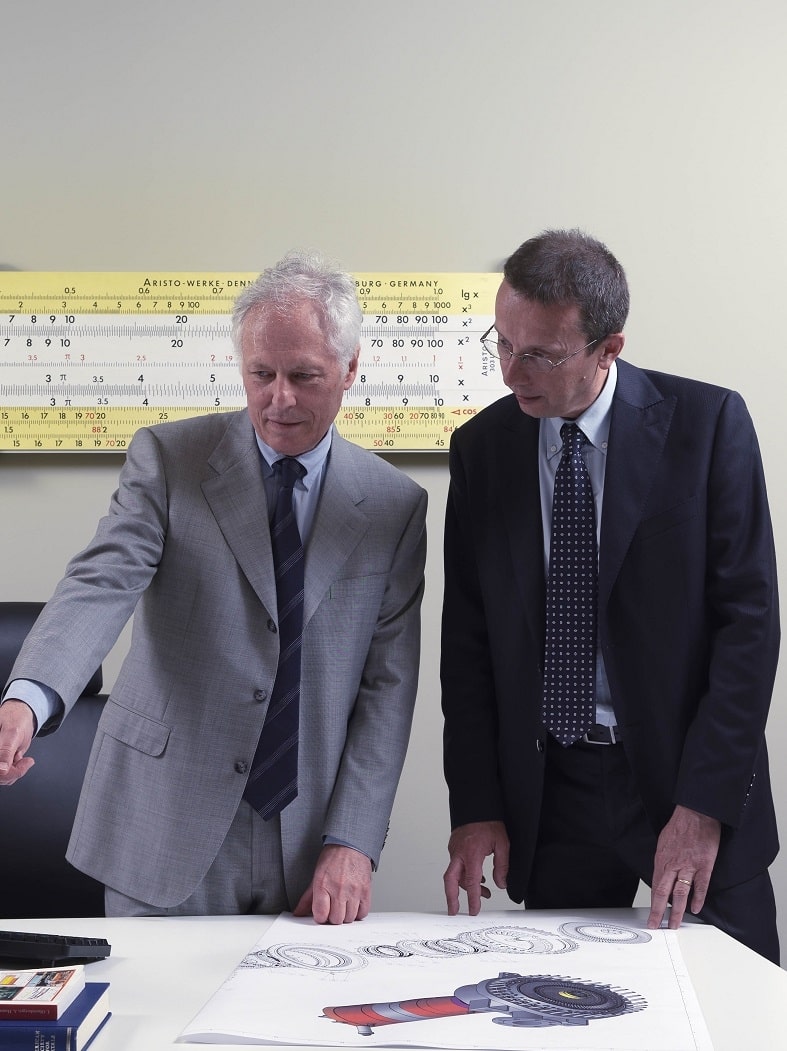
FEATURES
The ORC unit is a system based on a closed-loop thermodynamic cycle for the generation of electric and thermal power, especially suitable for distributed generation. In this section the key points of ORC technology compared to steam technology are explained.
- Large range of sizes from small to medium sizes (up to 40 MW per single shaft)
- Different primary energy sources, from renewable energy (geothermal, solar, biomass) to energy efficiency (i.e. waste heat from industrial processes) to conventional fuels (natural gas, flare gas)
- Different kind of heat carrier fluids: intermediate fluid (thermal oil, saturated steam, water) or directly from industrial smoke through a direct exchange
- Large rangeability: different temperatures of the source (even below 100°C through selection of proper working fluid); partial load (the ORC system keeps high electrical efficiency even when operating with lower thermal power input, even 10% of the nominal one)
* The efficiency of the ORC system is always optimized: on average at 50% load, electrical efficiency is still 90% of the nominal electrical efficiency.
- Cogeneration mode or power-only mode. In cogeneration, the thermal output can be hot water or steam
- Ease of integration into pre-existing systems (i.e. in waste heat recovery from industrial processes)
- Island mode capability
- Simple technical features: low pressures involved, low speed turbine, limited number of stages of the turbine (≤6), self-lubricating fluids, no water required
- Easy and cost-effective operation & maintenance: automatic operation (no qualified operator required), minimal maintenance activities, no major overhaul (turbine not subject to erosion and corrosion), fast start-stop procedures, no chemical and water treatments, low refiling of fluid required
- Possibility to install the ORC unit in remote places, working efficiently
- High availability (98% +)
- Long life
- Core system for renewable energy and energy efficiency
- Clean generation of power and heat
- Reduction of CO2 emissions (e.g. in heat recovery or in geothermal where the ORC system operates with zero emissions thanks to the reinjection)
INNOVATION
Turboden has always been oriented to innovation and R&D and has always had a strong connection with the academic research. The company is a pioneer in ORC technology thanks to the design and the manufacturing of experimental ORC plants such as the first solar thermodynamic ORC unit in 1984, the experimental heat recovery ORC power plant in 1996 and the first biomass ORC unit in 1998. Turboden has an internal Research & Development Centre, working on fluid dynamics and thermodynamics to continuously improve the performance of its ORC units. Contributions and ideas by employees, most of them engineers, are encouraged by the management and help greatly to improve Turboden plants' design and manufacturing.
THE TURBINE
More than 60 different axial turbines were designed and realized for various projects, from 2 to 6 stages reaching up to 40 MW of power and in some cases exceeding isentropic efficiency 90%.
WORKING FLUIDS
More than 10 different working fluids have been used by Turboden to date, e.g. silicon fluids, hydrocarbons, old and new generation refrigerants, depending on the application. Over time and through an important R&D effort, Turboden has developed a deep understanding of fluid properties, thermal stability and flammability, key factors in the decision on the best fluid for each specific application. A successful ORC installation begins with the right fluid selection.
OPERATING TEMPERATURES
Turboden unique knowledge of fluids and attitude to innovation have allowed to increase operating temperature continuously, improving efficiency levels in power only and CHP configurations. Today turbine inlet temperature exceeding 300°C is standard technology, a further confirmation of Turboden leadership in its field.
The latest development of Turboden is in biomass application, where a new ORC unit operates at very high temperatures (about 400°C) either in CHP mode (generating medium pressure steam to feed industrial users), or in power only solution (exceeding 30% gross electric efficiency).
HISTORICAL NOTES
The Rankine cycle is named after William John Macquorn Rankine (July 5, 1820 - December 24, 1872), a Scottish engineer and physicist. He was a founding contributor to the science of thermodynamics. Rankine developed a complete theory of the steam engine and indeed of all heat engines. His manuals of engineering science and practice were used for many decades after their publication in the 1850s and 1860s. He published several hundred papers and notes on science and engineering topics, from 1840 onwards, and his interests were extremely varied, including, in his youth, botany, music theory and number theory, and most major branches of science, mathematics and engineering. He was an enthusiastic amateur singer, pianist and cellist who composed his own humorous songs.
The Rankine cycle is usually based on water as a working fluid. Applications of the cycle with different working fluids started to appear soon, such as the Naphtha boats. In 1883 Frank Ofeldt developed a unique power system which he hoped would have replaced steam. His naphtha engines are steam engines that boil naphtha (a form of gasoline) instead of water to drive the pistons. At the time, the government required a license to boil water in steam engines, but did not require one to boil gasoline. Therefore, for the first time a gentleman boater could operate his own power boat without the assistance of an engineer. One would have to be of "gentleman's" means to own one of these vessels. In the 1880s, a 21 foot boat with a Naphtha engine cost $750 - one and a half times the annual wage of craftsmen who built them (from the Mystic Seaport Museum website).
The Organic Rankine Cycle technology was seriously developed only during the XX century. In Italy, an experiment was carried out during the Thirties on the Island of Ischia. Important studies were conducted after the Second World War in Russia, USA and Israel. Back to Italy, during the Seventies the Italian ORC School was born at the Politecnico di Milano, Italy's most important engineering University. Its founder was Prof. Gianfranco Angelino, with his colleagues Prof. Ennio Macchi and Prof. Mario Gaia, the founder of Turboden.
Organic Rankine Cycle is a well-known and widely spread form of energy production, mostly in biomass and geothermal applications, but great rises in solar and heat recovery applications are also expected. Environmental concern over climate change and floating oil and gas prices are powerful reasons supporting the growth of this efficient, clean and reliable way of producing electricity.
All Turboden Solutions
ENERGY EFFICIENCY
RENEWABLES
